Automatisch von KI übersetzt, Original lesen
Fraco bringt Innovationen für Renovierungsarbeiten in Montreal auf den Markt
13 Februar 2025
Der fast 60 Jahre alte, 189 Meter hohe Börsenturm von Montreal musste kürzlich umfassend renoviert werden.
Der Wolkenkratzer wurde 1964 für die kanadische Expo 67 erbaut und ursprünglich im International Skyscrapers Architectural Style errichtet. Er zeichnet sich durch eine bronzefarbene, eloxierte Aluminium-Vorhangfassade aus, die einen starken Kontrast zu den leicht geneigten Betonfertigteilstützen an den Ecken bildet. Die dreistöckigen Maschinengeschosse mit vertieften achteckigen Ecken unterteilen die Fassade in drei Abschnitte, sodass hinter den Stützen auf diesen Ebenen kleine Freiflächen entstehen.
Die vorgefertigten Betonplatten (mit einem Gewicht von 1.360 bis 3.260 kg) an den Gebäudeecken sowie die Anker, mit denen diese Platten am Gebäude befestigt waren, mussten ersetzt werden. Darüber hinaus waren Reparaturen an der Spitze der Betonplatten aufgrund erheblicher Beschädigungen notwendig.
Angesichts einer Reihe von Herausforderungen, die von der Form und Lage des Gebäudes bis hin zum örtlichen Wetter und dem Gewicht von Material und Ausrüstung reichten, war eine maßgeschneiderte Lösung erforderlich – und Fraco kam dieser Aufforderung nach.
Die wesentlichen Details
Die größten Herausforderungen des Projekts waren der Standort, die Mieter und Immobilienwerte des Gebäudes, die Wetterbedingungen, das Gewicht des zu verbauenden Materials und die Form des Gebäudes.
Der Standort spielte für das Projekt eine Schlüsselrolle, nicht nur aufgrund der erstklassigen Lage des Wolkenkratzers in der Innenstadt, wo es von Menschen und Unternehmen wimmelt, sondern auch aufgrund dessen, was sich unter den Straßen abspielt, die er teilt.
Unter dem Börsenturm befinden sich in mehreren unterirdischen Ebenen verschiedene Funktionen – Serverräume, ein Einkaufszentrum mit Anschluss an eine U-Bahn-Station, ein Parkplatz und vieles mehr.
In der komplexen Umgebung der mehrstöckigen unterirdischen Stadt stellte die Sicherung der Basis von Fracos Plattform eine Herausforderung dar. Da eine Last von voraussichtlich 160.000 Kilogramm auf den Boden übertragen werden musste, bestand bei direkter Platzierung auf der Oberfläche die Gefahr eines Einsturzes der unterirdischen Infrastruktur. Um die Stabilität und Sicherheit der Plattform zu gewährleisten, war eine Lösung dieses Problems unerlässlich.
Für die Mieter des Turms waren ein Umzug und die damit verbundene Beeinträchtigung ihres Alltagslebens keine Option. Die Arbeiten mussten außerhalb der Geschäftszeiten und nachts geplant werden. Bei einer Projektlaufzeit von rund vier Jahren mussten zudem die Wetterbedingungen – wie Feuchtigkeit, Schnee, Sonne, Regen und Wind – berücksichtigt werden.
Die Lösungen von Fraco mussten außerdem dem Transport von Platten mit einem Gewicht von bis zu 3.260 kg standhalten – da das Gebäude neben anderen Hochhäusern liegt, konnte kein Kran eingesetzt werden.
Und schließlich die Form. Die Basis des Börsenturms ist nach oben hin etwas breiter und verjüngt sich auf etwa 2,4 Meter. Die vorgefertigten Platten an der Basis waren deutlich größer und schwerer als die an der Spitze.
Um den externen Zugang zum voll belegten und funktionsfähigen Bürogebäude zu ermöglichen, konstruierte, produzierte und installierte Fraco drei maßgeschneiderte, dreitürmige Mastkletterbühnen mit jeweils einem selbstaufrichtenden Ausleger auf der Spitze der drei Masten. Fracos Standard-SEP-Transportbühnen nutzten die Dreimastkonstruktion für den Transport von Material und Arbeitern zur Baustelle.
Um diese Herausforderungen zu meistern, hat Fraco mehrere Ziele zur Beseitigung der Zugangshindernisse festgelegt. Das erste Ziel war die Entwicklung einer innovativen technischen Lösung für eine Plattform, die:
- sich effektiv an Gebäudeecken auf und ab bewegen
- tragen schwere Lasten
- Betrieb ohne Kran
- ermöglichen eine einfache Mobilität zwischen den Ebenen
- Gewährleistung der Sicherheit der Arbeitnehmer und der Arbeitseffizienz
- „veränderbare“ Arbeitsflächen, um nah an der verjüngten Fassade zu bleiben
Das zweite Ziel bestand darin, das Basisproblem anzugehen, und das dritte Ziel bestand darin, wetterbedingte Probleme zu mildern.
Wie Fraco es gemacht hat
Entwicklung einer technischen Lösung für die Plattform:
Die anfängliche Herausforderung bestand darin, eine mastgestützte Arbeitsbühne zu entwickeln, die die Gebäudeecken formen und gleichzeitig Stabilität, Sicherheit und ausreichende Tragfähigkeit gewährleisten kann. Fraco löste diese Herausforderung mit der Entwicklung einer Drei-Turm-Plattform, die zwei FMC-8-Plattformen mit einer speziellen Bodenverbindung – einem absenkbaren Arbeitsbereich – verbindet. Diese Lösung ermöglichte die Trennung der Plattformen für vertikale Bewegungen und deren anschließende Remontage auf der gewünschten Höhe. Die mit einem modularen Traversensystem ausgestattete Verbindungseinheit verfügte über einen anpassbaren Arbeitsbereich, der sich an die sich verändernde Gebäudeform anpasste.
Die neue Anlage verfügte über ein umfassendes Sicherheitssystem zum Schutz von Personen und Gegenständen. Die Plattform war mit einem zwei Meter hohen, vollständig geschlossenen Geländer zum Schutz der Arbeiter ausgestattet. Der verstellbare Boden der Plattform reichte bis nahe an das Gebäude heran, um herabfallende Gegenstände zu verhindern. Die Sicherheitsvorrichtungen an beiden Anlagen schützten die Plattform vor einem freien Fall.
Die zweite Herausforderung bestand darin, einen geeigneten Hebemechanismus zu finden und zu integrieren, der sowohl die Errichtung der Türme als auch das Anheben der schweren Fertigteilplatten auf die gewünschte Höhe ermöglichte. Der Generalunternehmer zögerte aufgrund der Kosten, des begrenzten Platzes im Stadtzentrum und der Wetterbedingungen, einen Standardkran einzusetzen. Fracos Lösung bestand in einem selbstaufrichtenden Auslegerarm, der zur Installation der Türme und zur Handhabung der Betonfertigplatten eingesetzt wurde.
Fraco konstruierte eine spezielle Plattform für den selbstaufrichtenden Auslegerarm, die ausreichend Platz für eine wetterfeste Kabine für den Bediener bot. Dieser Auslegerarm erleichterte nicht nur die Turmmontage für Mastkletterbühnen, sondern minimierte auch den Platzbedarf und bot ausreichend Kraft, um die 3200 kg schweren Fertigteilplatten sicher anzuheben. Der Auslegerarm bewegt sich mithilfe eines ebenfalls von Fraco entwickelten hydraulischen Ratschensystems auf und ab.
Standortbezogene Herausforderungen bewältigen
Unter der Innenstadt von Montreal erstreckt sich eine ausgedehnte unterirdische Stadt mit mindestens fünf Stockwerken unter dem Börsenturm. Die Platzierung der Plattform ohne Bodeneinsturzgefahr stellte eine große Herausforderung dar.
Dieses Problem wurde durch die strategische Installation von Stützpfosten in den Untergeschossen gelöst. Anschließend wurden mehrere massive Stahlträger im Erdgeschoss positioniert, um das Gewicht der Plattform effektiv auf das Gebäudefundament zu verteilen. Die Träger ruhten auf dem verstärkten Betonfundament des Börsenturms. Diese komplexe Konstruktion erforderte angesichts der hohen Anforderungen präzise Berechnungen.
Bewältigung wetterbedingter Herausforderungen
Um die dritte wetterbedingte Herausforderung zu bewältigen, entwickelte Fraco einen Zugang zum Sarkophag, der die im Bau befindlichen Ebenen schützen sollte.
Das Gebäude war im Wesentlichen in mehrere „Arbeitszonen“ mit jeweils sechs Stockwerken unterteilt. Die im Bau befindlichen Stockwerke wurden von einem Sarkophag umschlossen, der erstens dafür sorgte, dass das Innere des Gebäudes nicht durch Witterungseinflüsse beschädigt wurde, und zweitens die Arbeiten vor extremer Kälte und Hitze schützte.
Im Sarkophag rissen die Arbeiter die alten Betonblöcke ab und transportierten den Schutt mithilfe der Fraco SEP-Transportplattform ab. Anschließend ersetzten sie die Stahlanker, mit denen die Platten am Gebäude befestigt waren. Anschließend wurden neue massive Fertigteilplatten mithilfe des selbstaufrichtenden Auslegerarms auf die Plattform befördert. Nach dem Austausch der Betonfertigteile senkten sich die Arbeitsplattform und die Auslegerplattform sechs Stockwerke ab. Auch der Sarkophag wurde abgesenkt.
Mastkletterarbeitsbühnen setzen sich durch
Die maßgeschneiderte MCWP wurde speziell für dieses Projekt entwickelt und gefertigt. Die Plattform bestand aus zwei FMC-8-Plattformen, die für sicheres und effizientes Arbeiten miteinander verbunden, während der vertikalen Bewegung jedoch leicht getrennt werden konnten. Der verstellbare Boden ermöglichte die Anpassung der Gebäudeecken. Mehrere Sicherheitsvorrichtungen wurden implementiert, um die Sicherheit der Personen zu gewährleisten und den Zusammenbruch der Einheit zu verhindern.
Um den Einsatz eines Krans zu vermeiden, montierte Fraco oben auf dem Mast einen selbstaufrichtenden Auslegerarm. Dieser konnte die Masttürme für die Montage der Plattformen anheben und war stark genug, um die 3.250 kg schweren Fertigteilplatten sicher zu heben. Der Fraco SEP-Bauaufzug, der an derselben Dreimastkonstruktion betrieben wurde, diente ebenfalls dem sicheren Transport von Personen und Material.
Der selbstaufrichtende Auslegerarm, der auf seiner vorgesehenen Plattform positioniert ist, reduziert nicht nur die Kosten und Unannehmlichkeiten eines herkömmlichen Baukrans in der Innenstadt, sondern ermöglicht auch die Errichtung von Türmen für Mastkletter- und Transportplattformen. Er sparte im Vergleich zu herkömmlichen Gerüsten Monate und im Vergleich zum Einsatz eines Baukrans Wochen, da die Nähe des Auslegerarms zum Arbeiter eine direkte Materialhandhabung ermöglicht und so die Arbeit deutlich beschleunigt. Darüber hinaus trug seine Präzision maßgeblich zur Geschwindigkeit und Sicherheit der Arbeiten bei.
Auch das Motorsystem der Plattform mit dem selbstaufrichtenden Auslegerarm musste bestimmte Kriterien hinsichtlich Gewicht, Standort, Sicherheit, Geschwindigkeit und Leistung erfüllen.
Um diesen Problemen zu begegnen, entwickelte und fertigte Fraco zudem ein hydraulisches Ratschensystem. Dieses System verfügte über eine hydraulische Komponente für den Transport schwerer Lasten, während die mechanische Komponente für die Sicherheit sorgte. Alle drei Motorblöcke waren zudem jeweils mit zwei hydraulischen Ratschenmechanismen ausgestattet. Ein Mechanismus diente dazu, den Kletterblock an Ort und Stelle zu halten, während der andere als beweglicher Teil fungierte. Diese Mechanismen kuppelten abwechselnd ein und aus, jeweils einzeln.
Die Ingenieure von Fraco implementierten zudem eine zusätzliche Sicherheitsfunktion. Jeder unabhängige Mechanismus verfügte über eine eingebaute elektrische Sicherheitsvorrichtung. Diese verhinderte das Auskuppeln, bis das Gegenstück vollständig eingekuppelt war, und verhinderte so eine Fehlbedienung durch den Bediener.
Für seine Arbeit und Innovationen wurde Fraco 2024 von der Scaffold & Access Industry Association mit dem Preis „Projekt des Jahres“ für mastbetriebene Hebezeuge und Arbeitsbühnen ausgezeichnet. Weitere Informationen zu diesen begehrten Auszeichnungen finden Sie unter www.saiaonline.org.
STAY CONNECTED
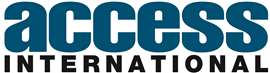
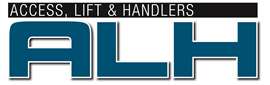

Receive the information you need when you need it through our world-leading magazines, newsletters and daily briefings.
KONTAKTIEREN SIE DAS TEAM
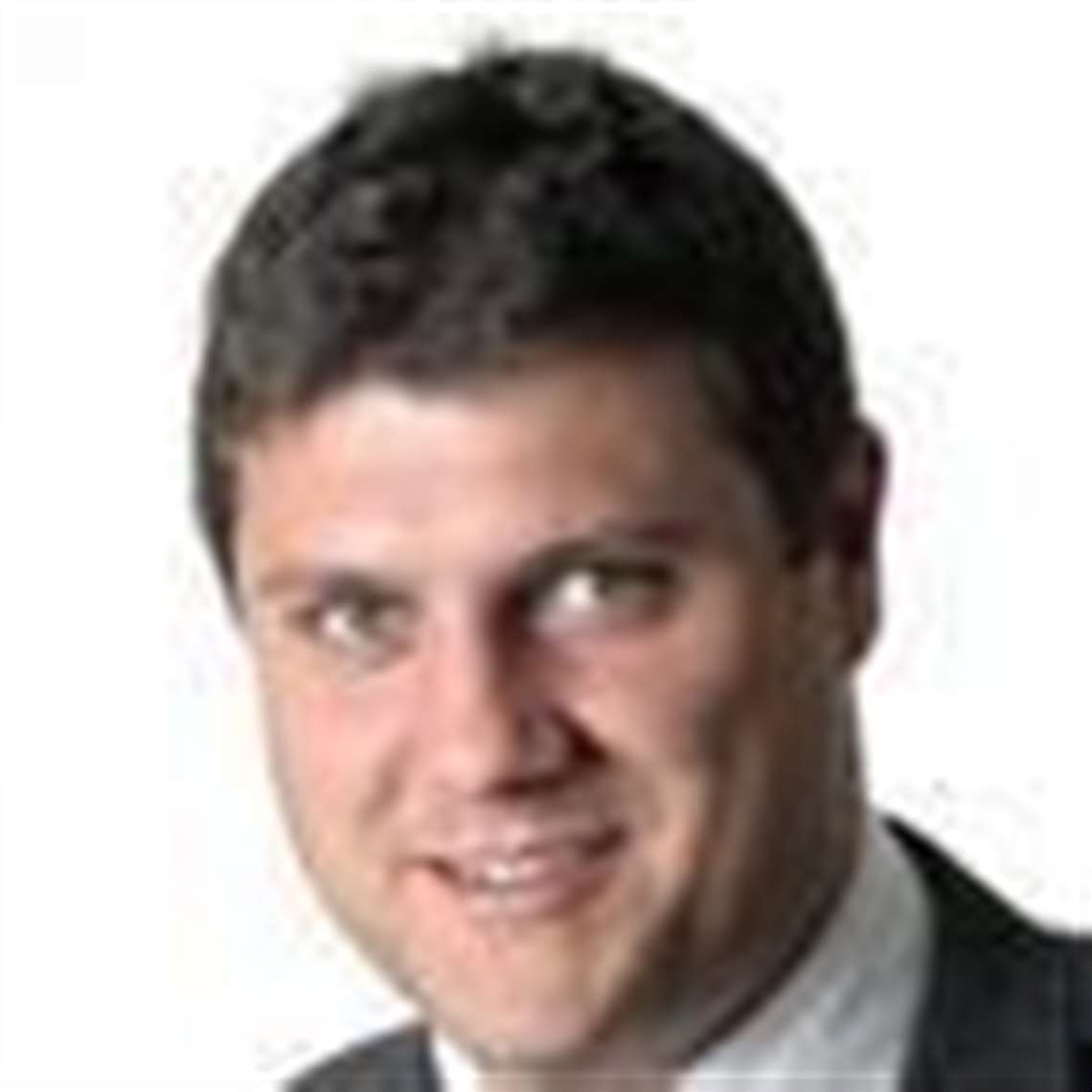
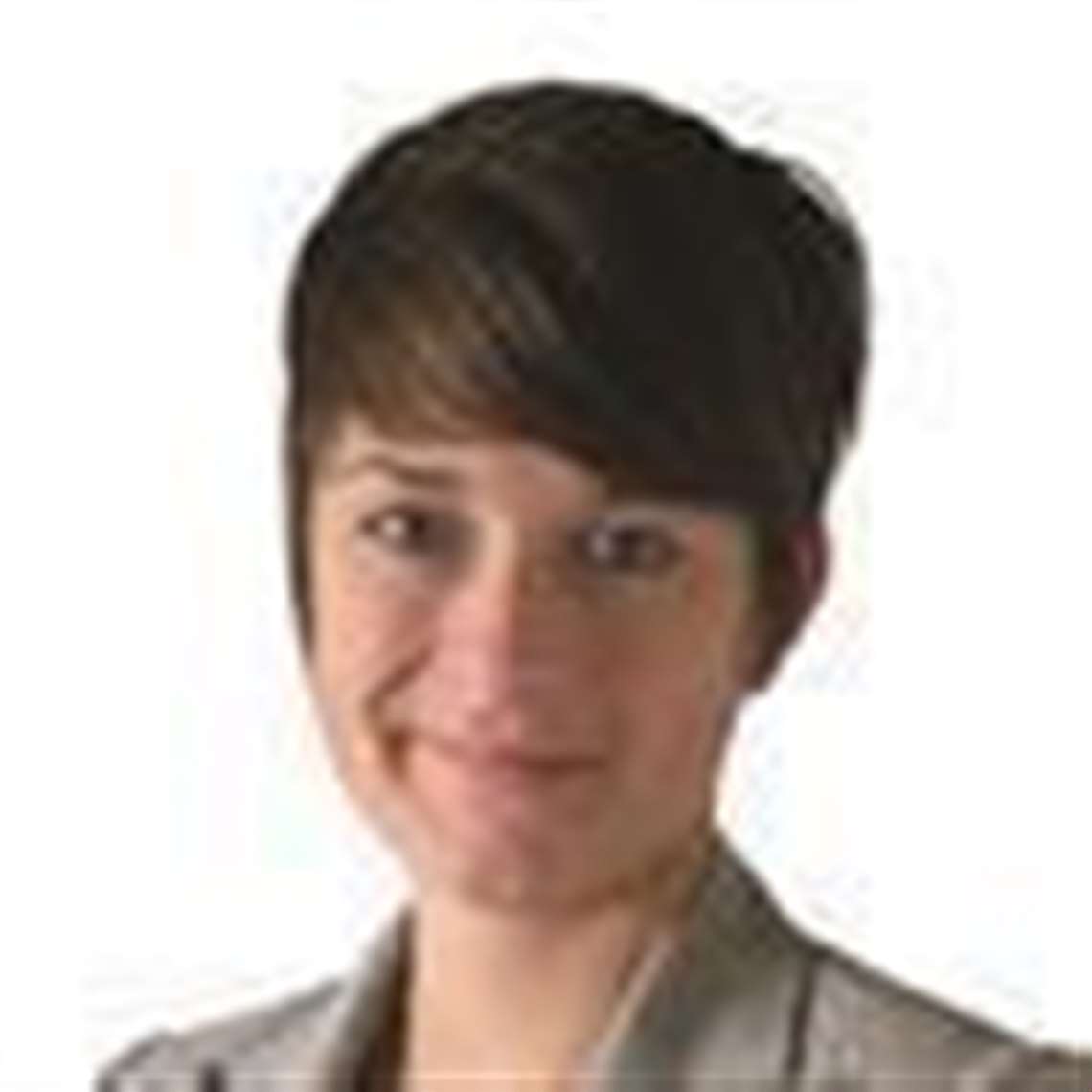
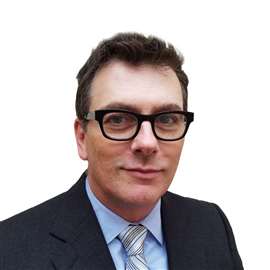
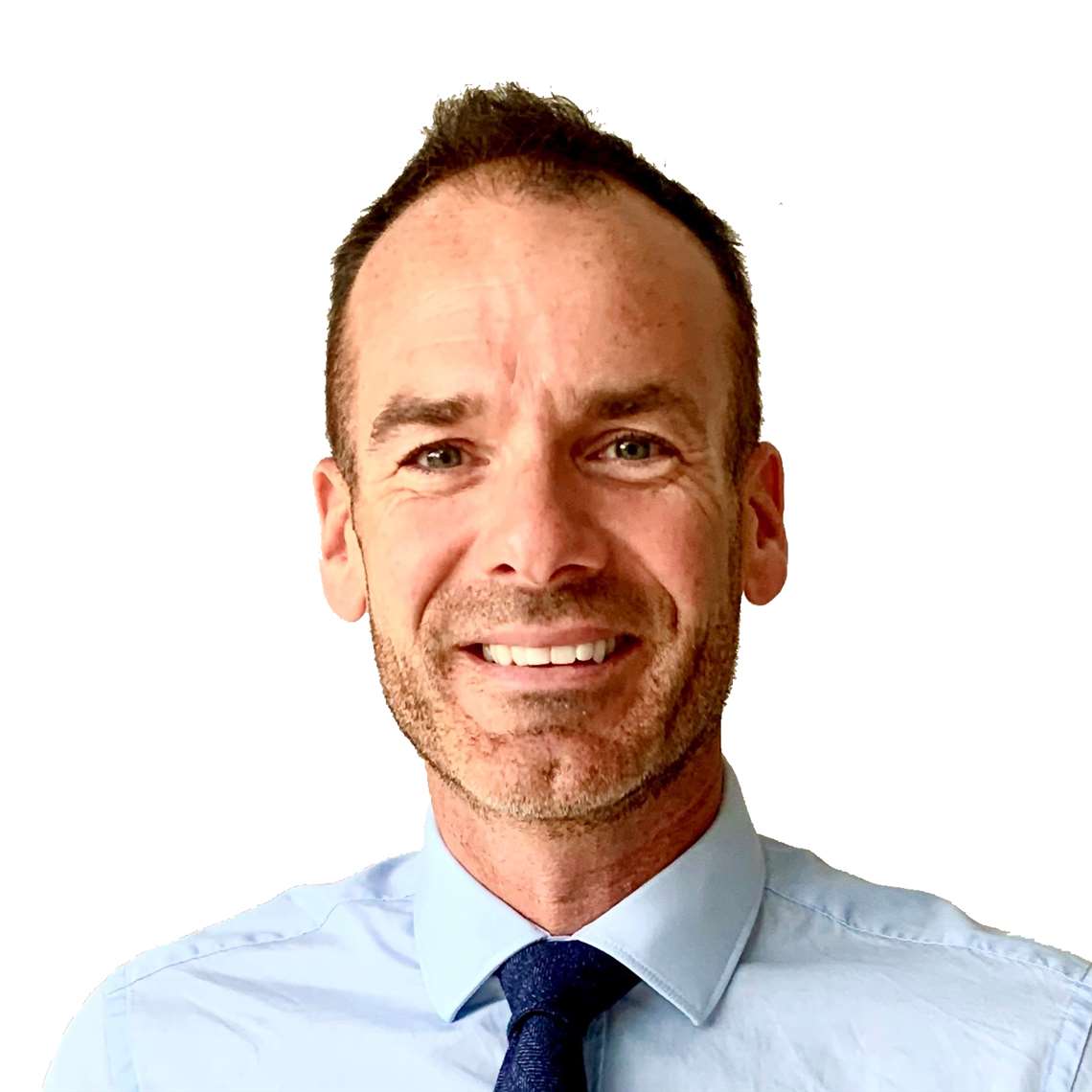