Fraco innova per la ristrutturazione di Montreal
13 febbraio 2025
Con quasi 60 anni di storia, la Torre della Borsa di Montreal, alta 187 metri, ha recentemente richiesto importanti lavori di ristrutturazione.
Costruito nel 1964 per l'Expo 67 canadese, il grattacielo fu originariamente costruito nello stile architettonico internazionale dei grattacieli, caratterizzato da una facciata continua in alluminio anodizzato color bronzo che contrasta nettamente con le colonne prefabbricate in cemento armato leggermente inclinate agli angoli. Diviso in tre sezioni da solai meccanici con angoli ottagonali arretrati, lascia spazio a piccoli spazi aperti dietro le colonne a questi livelli.
I pannelli prefabbricati in calcestruzzo (del peso di 1.360-3.260 kg) sugli angoli dell'edificio e gli ancoraggi che li fissavano all'edificio dovevano essere sostituiti. Inoltre, si rendevano necessarie riparazioni alla punta delle solette in calcestruzzo a causa del suo significativo degrado.
Considerate le numerose sfide che andavano dalla forma e dalla posizione dell'edificio alle condizioni meteorologiche locali, fino al peso dei materiali e delle attrezzature, era necessaria una soluzione personalizzata e Fraco ha risposto alla chiamata.
I dettagli essenziali
Le principali sfide del progetto erano la posizione, gli inquilini dell'edificio e il valore delle proprietà, le condizioni meteorologiche, il peso del materiale da installare e la forma dell'edificio.
La posizione ha giocato un ruolo fondamentale nella narrazione del progetto, non solo perché il grattacielo si trova in una posizione privilegiata nel centro della città, brulicante di gente e attività commerciali, ma anche per ciò che avviene sotto le strade cittadine con cui condivide la stessa posizione.
Sotto la Torre della Borsa, diversi livelli sotterranei ospitano varie funzioni: sale server, un centro commerciale collegato a una stazione della metropolitana, un parcheggio e molto altro ancora.
Nel complesso contesto della città sotterranea a più livelli, la sicurezza della base della piattaforma Fraco si è rivelata una sfida. Con un carico previsto di 175.000 kg da trasferire al suolo, posizionarla direttamente in superficie rischiava di causare un potenziale crollo dell'infrastruttura sotterranea. Trovare una soluzione a questo problema era fondamentale per garantire la stabilità e la sicurezza della piattaforma.
Per gli inquilini della Torre, il trasferimento e l'interruzione della vita quotidiana non erano opzioni. I lavori dovevano essere programmati per le ore notturne e notturne. E con una durata del progetto di circa 4 anni, si dovevano tenere in considerazione le condizioni meteorologiche, con il continuo fluire di umidità, neve, sole, pioggia e vento.
Le soluzioni di Fraco dovevano inoltre essere in grado di sopportare la movimentazione di pannelli dal peso di circa 7.000 libbre: non era possibile utilizzare una gru a causa della posizione dell'edificio accanto ad altre strutture di grandi dimensioni.
E infine, la forma. La base della Torre della Borsa è leggermente più larga verso l'alto, rastremandosi verso l'interno a circa 2,4 metri. I pannelli prefabbricati alla base erano significativamente più grandi e pesanti di quelli in cima.
Pertanto, per garantire l'accesso esterno all'edificio adibito a uffici, completamente occupato e operativo, Fraco ha progettato, prodotto e installato tre piattaforme autosollevanti personalizzate a tre torri, con un braccio automontante appoggiato sulla sommità di ciascuna delle tre torri. Le piattaforme di trasporto SEP standard di Fraco utilizzavano la struttura a tre torri per trasportare materiali e personale sul posto di lavoro.
Per affrontare le sfide, Fraco si è posta diversi obiettivi per superare gli ostacoli legati all'accesso. Il primo obiettivo era progettare una soluzione tecnica innovativa per una piattaforma in grado di:
- muoversi efficacemente su e giù per l'angolo dell'edificio
- supportare carichi pesanti
- operare senza bisogno di una gru
- facilitare la mobilità tra i livelli
- garantire la sicurezza dei lavoratori e l'efficienza del lavoro
- superficie del piano di lavoro 'modificabile'', per rimanere aderente alla facciata rastremata
Il secondo obiettivo era quello di risolvere il problema della base, mentre il terzo era quello di attenuare i problemi legati alle condizioni meteorologiche.
Come ha fatto Fraco
Elaborazione di una soluzione tecnica per la piattaforma:
La sfida iniziale era quella di sviluppare una piattaforma di lavoro autosollevante in grado di modellare gli angoli dell'edificio garantendo al contempo stabilità, sicurezza e una capacità di carico adeguata. Fraco ha affrontato questo problema progettando una piattaforma a 3 torri, unendo 2 piattaforme FMC-8 con un giunto specializzato a pavimento: un'area di lavoro a scomparsa per collegare entrambe le piattaforme. Questa soluzione ha permesso di separare le piattaforme per il movimento verticale e il loro successivo riassemblaggio ai livelli desiderati. L'unità di giunzione, dotata di un sistema di tralicci modulari, aveva un'area di lavoro personalizzabile per adattarsi alla forma mutevole dell'edificio.
La nuova unità includeva un sistema di sicurezza completo per prevenire la caduta di persone e oggetti. La piattaforma era dotata di un parapetto completamente chiuso alto 2 metri per proteggere i lavoratori, e il pavimento regolabile della piattaforma si avvicinava all'edificio per evitare la caduta di oggetti. I dispositivi di sicurezza di entrambe le unità proteggevano la piattaforma dalla caduta libera.
La seconda sfida consisteva nell'individuare e integrare un meccanismo di sollevamento adatto sia all'erezione delle torri che al sollevamento dei pesanti pannelli prefabbricati ai livelli desiderati. L'appaltatore generale esitava a utilizzare una gru standard a causa dei costi, dello spazio limitato in centro città e delle condizioni meteorologiche. La soluzione di Fraco è stata un braccio automontante, utilizzato per installare le torri e manipolare i pannelli prefabbricati in calcestruzzo.
Fraco ha costruito una piattaforma specializzata per il braccio automontante, con ampio spazio per ospitare una cabina di pilotaggio a prova di intemperie. Questo braccio non solo ha facilitato l'erezione della torre per le piattaforme autosollevanti, ma ha anche ridotto al minimo l'utilizzo di spazio a terra e ha fornito potenza sufficiente per sollevare in sicurezza i pannelli prefabbricati da 7.000 libbre (3.200 kg). Il braccio si muove verso l'alto e verso il basso utilizzando il suo sistema a cricchetto idraulico, anch'esso sviluppato da Fraco.
Affrontare le sfide legate alla posizione
Sotto il centro di Montreal si estende una città sotterranea tentacolare, con almeno cinque livelli sotto la torre della Borsa. Ciò ha rappresentato una sfida significativa nel posizionare la piattaforma senza rischiare il crollo del terreno.
Questo problema fu risolto installando strategicamente dei pali di sostegno nei piani interrati per fornire supporto. Successivamente, diverse massicce travi d'acciaio furono posizionate a livello del suolo per distribuire efficacemente il peso della piattaforma alle fondamenta dell'edificio. Le travi poggiavano sulle fondamenta in cemento armato della Torre della Borsa. Questa complessa opera ingegneristica richiedeva calcoli precisi, data l'elevata posta in gioco.
Affrontare le sfide legate al meteo
Per affrontare la terza serie di sfide legate alle condizioni meteorologiche, Fraco ha ideato un accesso al sarcofago che avrebbe dovuto proteggere i livelli in costruzione.
In sostanza, l'edificio era suddiviso in più "aree di lavoro", ciascuna composta da sei piani. I piani in costruzione erano racchiusi in un sarcofago che, in primo luogo, garantiva che le intemperie non danneggiassero l'interno dell'edificio e, in secondo luogo, proteggeva i lavori da freddo e caldo estremi.
All'interno del sarcofago, gli operai hanno demolito i vecchi blocchi di cemento e trasportato i detriti a terra utilizzando la piattaforma di trasporto Fraco SEP. Successivamente, hanno sostituito gli ancoraggi in acciaio che fissavano i pannelli all'edificio e, infine, nuovi pannelli prefabbricati di grandi dimensioni sono stati posizionati sulla piattaforma tramite il braccio automontante. Una volta sostituiti i blocchi di cemento prefabbricato, la piattaforma di lavoro e la piattaforma con braccio automontante sono scese di sei piani. E anche il sarcofago è stato abbassato.
Le piattaforme di lavoro autosollevanti prevalgono
La piattaforma di lavoro modulare (MCWP) personalizzata è stata progettata e realizzata appositamente per questo progetto. La piattaforma era costituita da due piattaforme FMC-8, che potevano essere unite per un lavoro sicuro ed efficiente, ma potevano essere facilmente separate durante il movimento verticale. Il pavimento regolabile permetteva di modellare gli angoli dell'edificio. Sono stati implementati diversi dispositivi di sicurezza per garantire la sicurezza delle persone e prevenire il crollo dell'unità.
Per evitare l'uso di una gru, Fraco ha installato sulla sommità dell'albero un braccio automontante in grado di sollevare le torri dell'albero per l'erezione delle piattaforme e sufficientemente potente da sollevare in sicurezza i pannelli prefabbricati da 7.000 libbre. Anche l'elevatore da cantiere Fraco SEP, installato sulla stessa struttura a tre alberi, è stato utilizzato per trasportare in sicurezza persone e materiali.
Il braccio automontante posizionato sulla piattaforma designata non solo ha ridotto i costi e gli inconvenienti derivanti dall'utilizzo di una gru da cantiere tradizionale in centro città, ma ha anche permesso di erigere torri per piattaforme di sollevamento e trasporto. Ha permesso di risparmiare mesi di lavoro rispetto ai ponteggi tradizionali e settimane rispetto all'utilizzo di una gru da cantiere, poiché la vicinanza del braccio all'operatore consente la manipolazione diretta dei materiali, accelerando significativamente i lavori. Inoltre, la sua precisione ha contribuito in modo significativo alla velocità e alla sicurezza delle operazioni.
Anche il sistema motore della piattaforma con braccio automontante doveva soddisfare determinati criteri di peso, posizione, sicurezza, velocità e potenza.
Per risolvere questi problemi, Fraco ha anche sviluppato e prodotto un sistema a cricchetto idraulico. Questo sistema prevedeva una componente idraulica per la movimentazione di carichi pesanti, mentre la parte meccanica garantiva la sicurezza. Inoltre, tutti e tre i blocchi motore erano dotati di due meccanismi a cricchetto idraulici ciascuno. Un meccanismo era dedicato al mantenimento in posizione del blocco di salita, mentre l'altro fungeva da parte mobile. Questi meccanismi si innestavano e disinnestavano alternativamente, uno alla volta.
Gli ingegneri di Fraco hanno inoltre implementato un'ulteriore funzione di sicurezza. Ogni meccanismo indipendente includeva un dispositivo elettrico di sicurezza integrato. Questo dispositivo impediva il disinnesto finché la controparte non fosse stata completamente innestata, prevenendo così un utilizzo improprio da parte dell'operatore.
Per il suo lavoro e le sue innovazioni, Fraco si è aggiudicata il premio "Progetto dell'Anno 2024" della Scaffold & Access Industry Association per la categoria "Piattaforme e montacarichi a colonna". Per maggiori informazioni su questi ambiti premi, visitate il sito www.saiaonline.org.
STAY CONNECTED
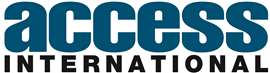
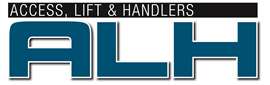

Receive the information you need when you need it through our world-leading magazines, newsletters and daily briefings.
CONTATTA IL TEAM
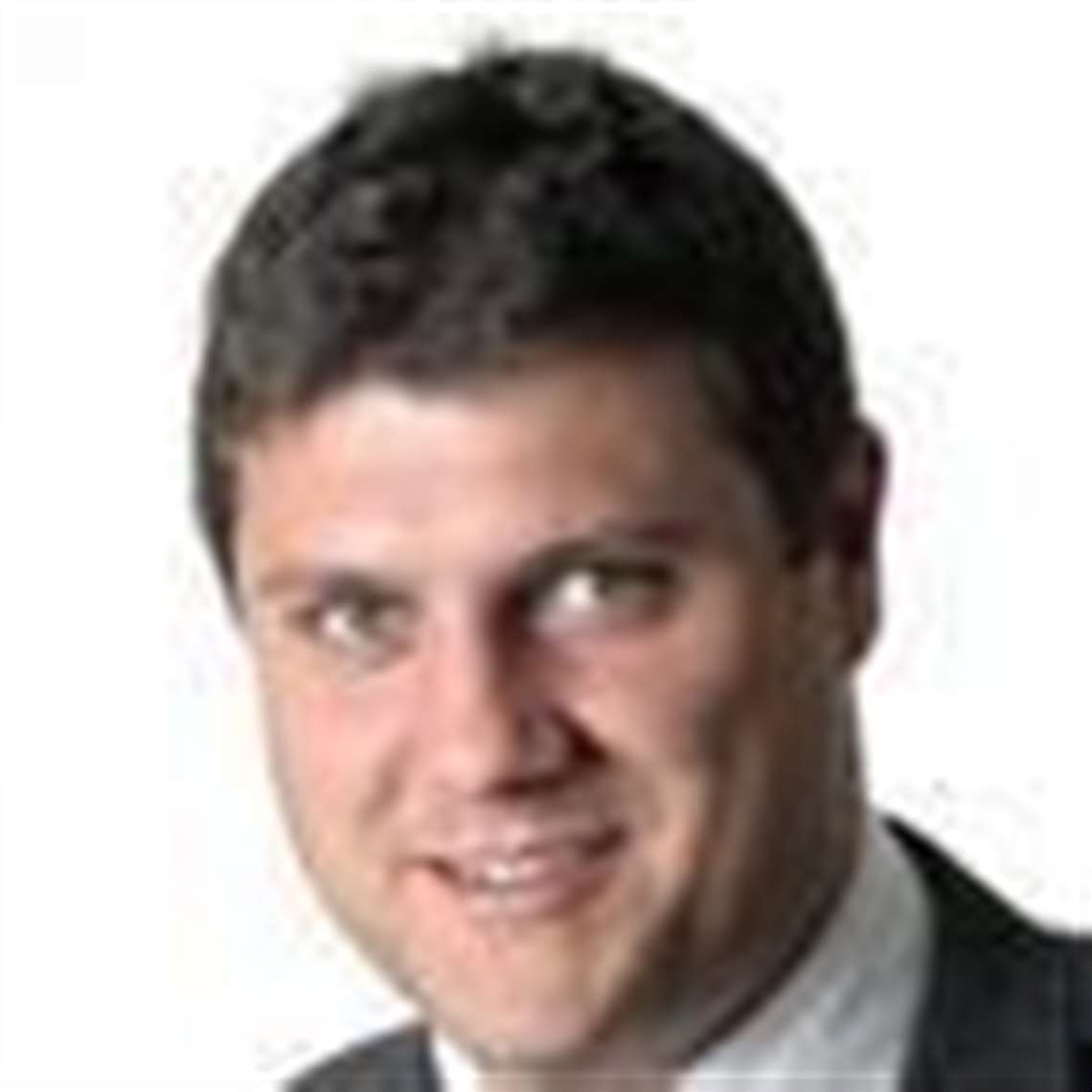
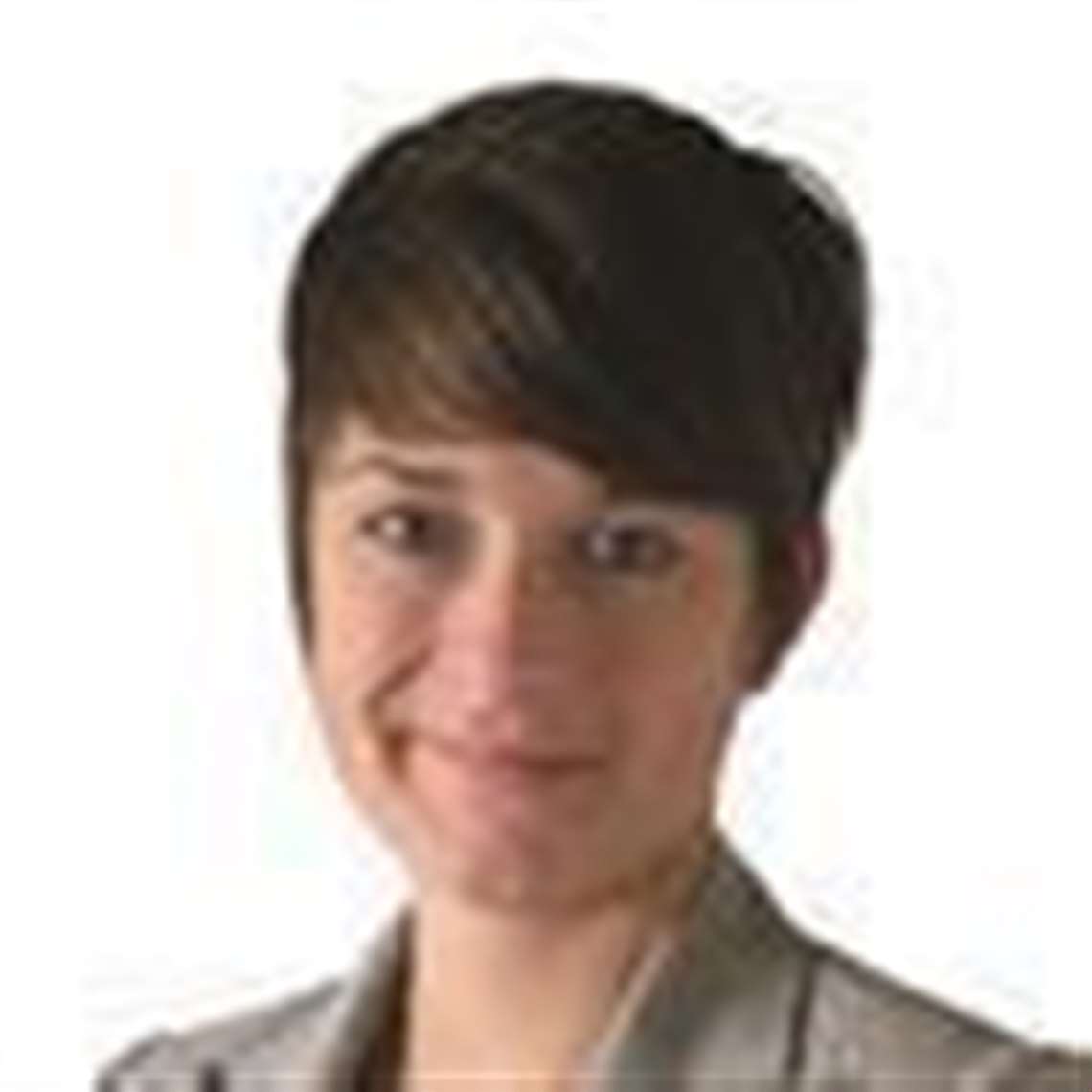
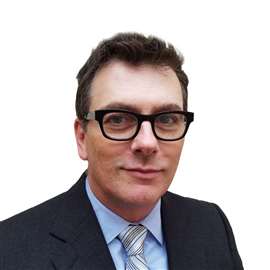
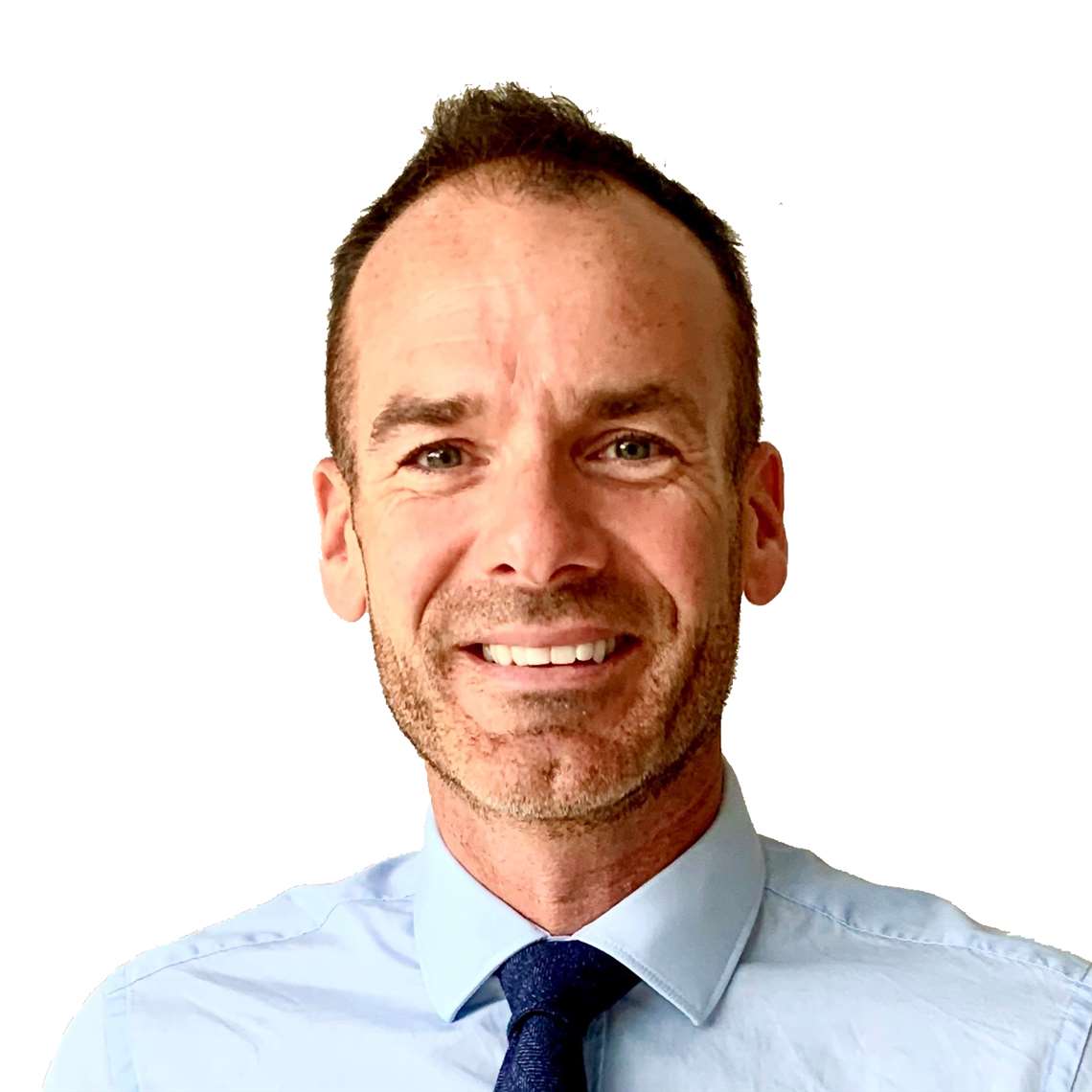