Design award for Tadano truck mount
26 August 2021
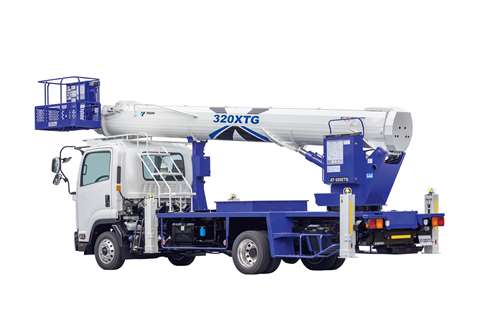
Tadano has won an industry design prize for its 32m working height AT-320XTG truck mounted platform.
The 51st Machine Industry Design Award was presented to the Japanese manufacturer by IDEA, an awards body supported by the Japanese Ministry of Economy, Trade and Industry, the Ministry of Education, Science and Technology and the Japan Patent Office and the Japan Chamber of Commerce. This is Tadano’s fourth Machine Design Award from IDEA, which was established in 1970.
Tadano said the award recognised the AT-320XTG’s combination of large crane and high working height technology to create what IDEA has termed “an unrivaled finish based on the safety of the boom weight reduction technology and the duplication of control equipment.”
Tadano president and CEO Toshiaki Ujiie attended the award ceremony, held at Keidanren Kaikan, on July 15th. He said, “In the continuing Covid pandemic, this prestigious award is a great encouragement for us.”
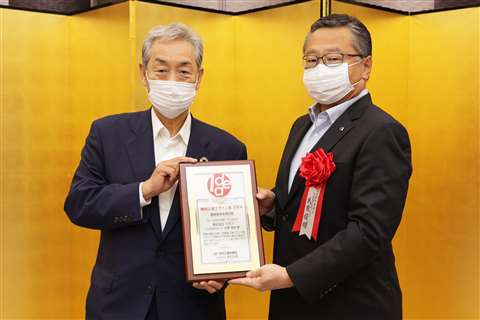
The 32m AT-320XTG, launched in January 2020, is also known as the Sky Boy. Its development began in 2016 on the heels of its predecessor, the AT-270TG. The AT-320XTG features the same vehicle weight and dimensions as the conventional 27m model, while achieving a higher maximum lifting height and working radius. The AT-320XTG’s maximum lifting height of 32m is the highest in its class in Japan, with a GVW of under 8 tonnes, meaning it can be driven with a medium-sized vehicle driving license.
It features a straight extending boom, redesigned from four sections to five. The boom’s redesign was one of the features recognised by IDEA. Tadano’s team used the latest structural research on weight reduction technology that had previously seen success in Europe. Incorporating this research, Tadano developed the first lightweight cross-section boom made of domestically produced thin plate high-strength steel, while also changing the boom shape from the conventional hexagon to a 21-sided polygon.
Redesigning the boom from four sections to five allowed extension of the total boom length, while incorporating a single telescopic cylinder means the five-stage boom opens simultaneously at a high speed. Installing electric wires and hydraulic hoses inside the boom avoids wear or damage and contributes to weight reduction and ease of maintenance by combining them with the built-in cylinders.
The Tadano team created a new, thinner boom steel plate, reducing thickness by half, from 4mm to 2mm, while increasing tensile strength to 1300MPa. The boom, with its 21 sides, is manufactured using an advanced steel sheet bending and welding process to ensure rigidity and strength.
Tadano engineers also made adjustments to the boom shape and shortened the straight parts of the cross-section to reduce welding strain and improve buckling strength. During initial testing, reverberations were detected along with wire noise not typically found in conventional booms. Pickup sensors and additional boom openings for visual inspections allowed the Tadano team to identify and solve these noise issues.
STAY CONNECTED
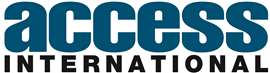
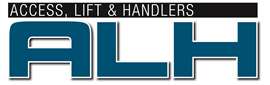

Receive the information you need when you need it through our world-leading magazines, newsletters and daily briefings.
CONNECT WITH THE TEAM
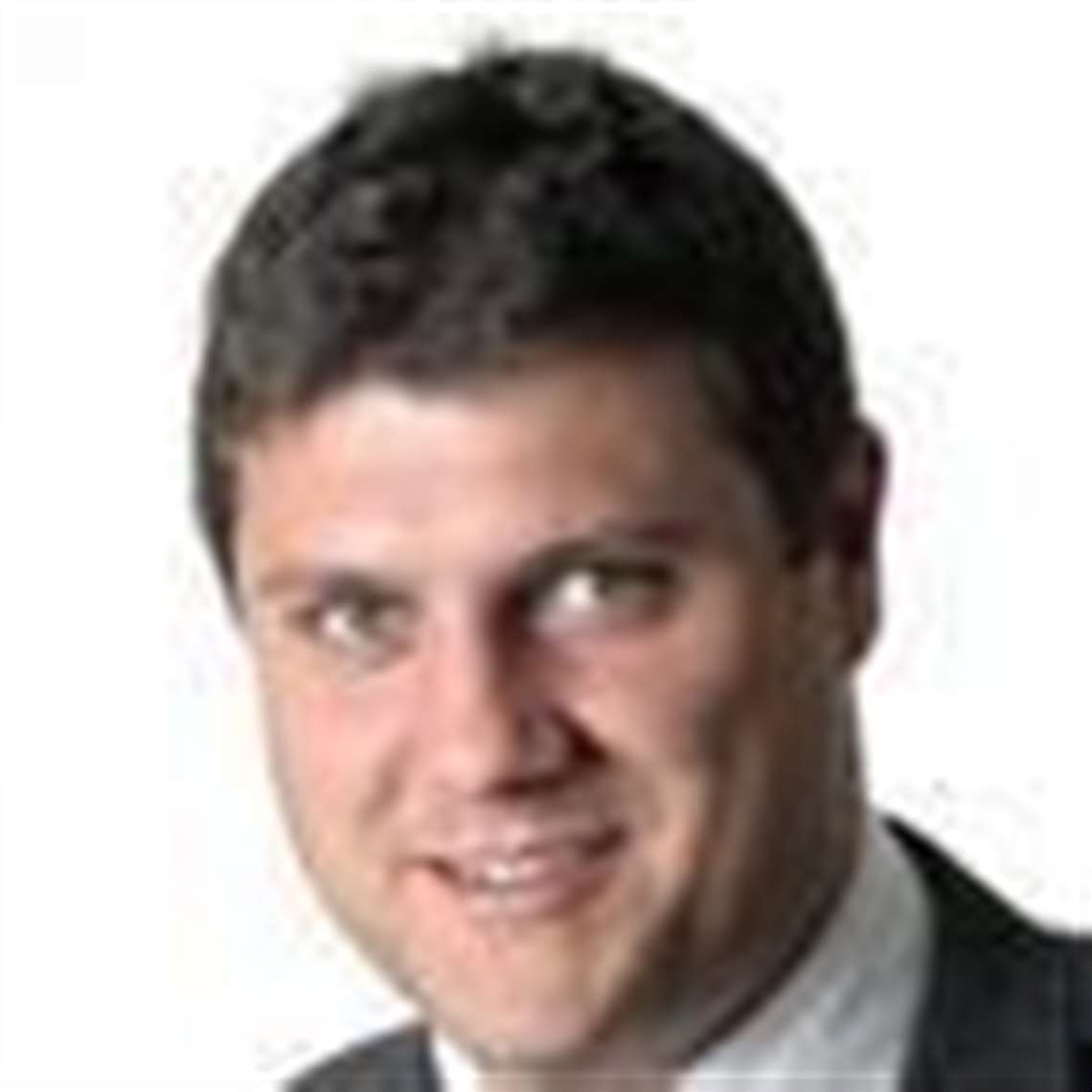
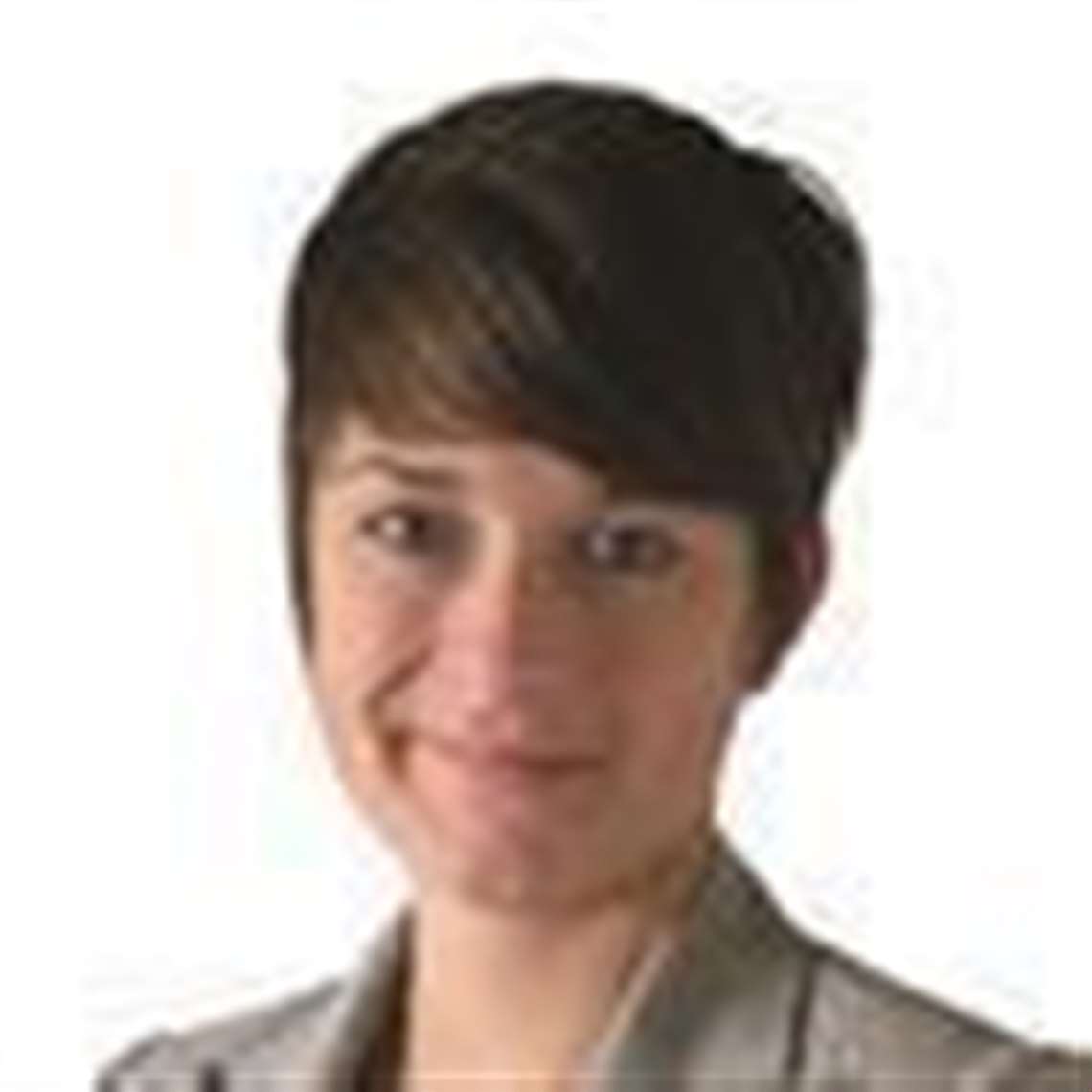
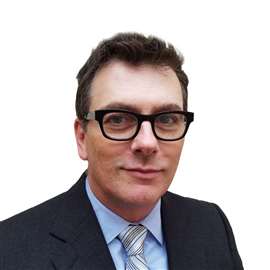
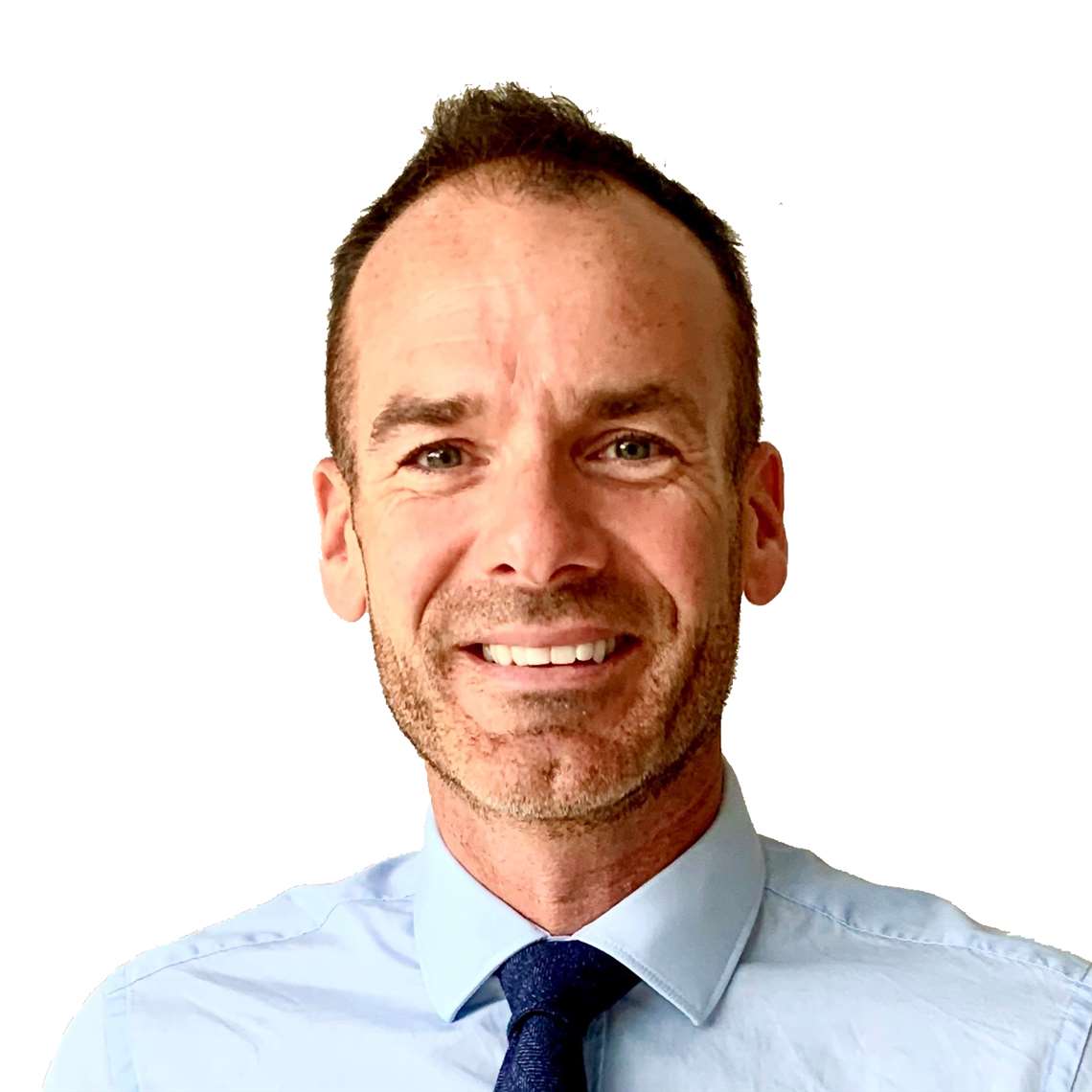